Most viticultural tasks, including pruning, canopy management and harvest are time sensitive with high labour requirements. With rising labour costs, and labour shortages, many producers are increasingly looking to machines for these essential practices. Mechanisation can offer timeliness and cost benefits, but it must be executed effectively. Jo Cowderoy finds out the advantages and challenges of mechanisation for canopy management.
“Labour is not only expensive but also becoming harder to find, so mechanisation and automation will help growers stay in business,” commented Luca Brillante, Bronco Wine Co. Chair in Viticulture and Assistant Professor, Department of Viticulture and Enology, California State University. “In fact, it is now well known that grapevines respond well to mechanised practices,” Luca Brillante added.
Vineyard mechanisation may reduce the need for labour – especially seasonal manual labour – but it also changes the calibre of vineyard staff required as operatives, managers or contractors need to have the skills and the experience necessary to set up and use the equipment effectively.
Equipment available
Mechanisation may not be suitable for all vineyard businesses, so capital costs and other options need careful consideration. “Depending on scale of the vineyard, it’s important to consider mechanisation, but it may be hard to justify for a one or two hectare vineyard and maybe more appropriate for an area of five hectares or more. However, it is possible to get cheaper equipment that might make mechanisation worthwhile for a smaller vineyard- the operation may just be slower,” explained Joel Jorgensen, Viticulture Director, Vinescapes Ltd.
“Most modern machines are capable of doing what is done by hand but at a greater speed thus reducing costs per hectare. However, the capital costs may be prohibitive, so contractors or machine hire should be considered,” commented David Sayell, Technical Advisor to Vitifruit Equipment.
“Leaf wall trimming and topping equipment is already fairly commonplace in the UK, mechanical leaf removal is increasingly being used, and now we are starting to see canopy lifting and tucking in machines – however, personally, I have concerns about the disposal of the plasticised twine used when it is removed at the end of the season,” said Joel Jorgensen.
“There are viable solutions for mechanical sucker removal,” commented Dr Glen Creasy, Viticulturist at Sabrosia SAS and Vigneron at Terre des 2 Sources, France. In fact, we’re using one on our vineyard now. It is a great time saver and means that the manual labour to do this, or herbicide use (contact herbicides to kill the suckers after selective spraying) can be eliminated.
“Mechanised shoot positioning and thinning systems exist, but these usually require specialised trellising systems, and they are not especially selective. However, they could be a viable option if the need is great enough. Until the development of cost-effective robots that can do lateral thinning and selective leaf removal (fruit removal and more) – options will be limited,” Glen Creasy added.
“Tucking in machines such as the Provitis PA5000 enable summer canopy lifting and tying in to replace manual wire lifting – and it’s a fast operation with a tractor. Of course, winter operations are vastly sped up with pre-pruning and cane pulling machines,” commented David Sayell.
“It’s imperative that experienced operators are encouraged to join the industry as they are sadly lacking. In my experience, as a supplier of machinery, it is often the case that far too much time is spent teaching tractor drivers how to use a tractor let alone the equipment they buy or hire. If growers wish to compete on price and quality with wine producers from around the world they must ‘tool up’ and ‘staff up’ to the same level of competence.
“When assessing future purchases of equipment take time to consider operator comfort and ease of use. Well-designed kit may be expensive to purchase initially but it will pay in the long run by increased output, timeliness, fewer breakdowns, a better quality job in the vineyard and a contented well motivated operator,” David added.
Advantages of mechanised operations
There can be many advantages to be gained from mechanisation, in the right situation. “Less costs and easier operations – as there is no need to manage a crowd of workers,” commented Luca Brillante. “There is also the timeliness of operation – at the right phenological time. It’s faster, which is useful when the time window is small – for example with rain forecasted. Also, with new technology operations can be more precise and adapted according to location of the machine in the field (variable rate) or plant size, with savings on inputs like fertilisers or sprays.”
“A large vineyard may need so many workers that mechanisation of tasks could cover the machinery investment quite quickly,” explained Joel Jorgensen. “Using the example of leaf removal – one worker may achieve 800-900 vines in a day, but a mechanical leaf remover will do five to seven hectares a day. This also means that timing of leaf removal can be more precise.
“As well as the financial benefits, another significant benefit of mechanisation is that one operator across the whole vineyard area will likely achieve more uniformed results compared to a large team of workers.
“Although precision viticulture does not necessarily need mechanisation or clever technology, it can support a good vineyard manager as it speeds up the data collection. This can result in better timing and more informed decision making,” added Joel.
“Increased mechanisation can give improved flexibility, especially when operations can take place at night, which might be beneficial from a timeliness aspect – for example, trimming or leaf removal before a spray is to be applied. It is also, invariably, quicker to do these jobs mechanically, especially when you take into account how much vineyard row can be worked on a per-person basis. The increased capital outlay can be an issue, however,” commented Glen Creasy.
David Sayell agreed: “Timeliness – and being able to cover large areas quickly when weather and soil conditions are favourable; you can also make best use of limited labour resources.”
Impact on crop quality and yield
Mechanisation can optimise crop yield and quality, depending on production goals and the skills of the vineyard manager. “Mechanisation can result in an increase in crop loads, especially when the best timing can be achieved for tasks such as trimming and leaf removal,” explained Joel Jorgensen. “Trimming results in uniformity of shoot length – if the number of leaves per shoot is similar and each shoot should be able to provide for its own fruit and it is easier to optimise yield. Also, correct timing and degree of leaf removal can benefit fruit set. Plus, some of the mechanical leaf removers will blow away detritus and caps – discouraging Botrytis. Opening the fruit zone improves sunlight, air movement, reduces humidity and improves the effectiveness of plant protection products – all helping to achieve a clean, healthy, disease free, quality crop,” Joel continued.
There are both positives and negatives, according to Glen Creasy: “Take leaf removal and even side trimming as an example; with some systems, berries and clusters can be damaged by the mechanical operation, leading to poor ripening, especially if the shoot carrying the cluster has been trimmed too close to the cluster – or to the possible entry of fungal disease organisms. With hand crews, this is much less likely to occur,” Glen added.
Disadvantages of mechanised operations
Mechanisation can provide efficiencies in production, but there are limitations to operational effectiveness. “Mechanisation demands quality staff with practical experience and a thorough grounding in tractor driving and implement operations and inexperienced staff are a big disadvantage,” commented David Sayell.
“You need skilled tractor drivers and operators of the machinery that also have a good understanding of the principles of the task,” agreed Joel Jorgensen. “For example, trimming is more than keeping the canopy tidy – its timing impacts the crop. So, the decisions on trimming will depend on the vineyard managers calculations of leaf to fruit ratios, canopy height and thickness, leaf layer numbers, and the ratio of mature to young leaves – understanding their source or sink roles,” Joel added.
“Machines are not as selective as a well-trained hand crew,” commented Glen Creasy. “There are always going to be areas where there is too much removed or not enough. This is true with a hand crew, too, but overall, the quality of the job should be better with well-trained people – that also have enough time to do the job correctly. Some things cannot, at this point, be done by machine for example the removal of interior leaves only. However, with the introduction of robots, this may be possible without the use of people in the future. There is the up-front cost of equipment to consider too,” added Glen.
Luca Brillante agreed: “Machines are non-selective and cannot adapt to variable conditions, so they work the best in uniform vineyards. Although this is changing with new technologies.”
“Planting density is also a consideration, as it is hard to mechanise a tightly spaced vineyard,” explained Joel. “A small tractor with a double-sided trimmer would be quite a weight over the root zone. If planning a vineyard that will be mechanised, it’s important to consider row spacing and ways to avoid compacting the root zone,” he added.
Environmental considerations
“I have some concerns with increased mechanisation as more tractor use means more passes over the soil and more diesel,” commented Joel Jorgensen. “Electric tractors are on their way, but not yet widely commercial – they will be brilliant, but of course still use energy. In the meantime, the newer diesel engines are cleaner and better, as are their gear boxes and engine management systems – improving efficiency.
“The best practice is to be very considered and make data-driven informed decisions with regards to tractor tasks to avoid unnecessary passes and reduce environmental impact – and save costs,” Joel added.
David Sayell added: “Use a tractor with modern emission control. Select an appropriate engine speed and gear.”
“There are many opportunities to do multiple operations per pass – mowing and trimming at the same time, for example,” suggested Glen Creasy. “Also reduce impact by using appropriately sized equipment and tractors for the job. Consider using renewable fuels so there is no net carbon release into the atmosphere. If climate-friendly electricity is available for purchase, then electric tractors will also be an option – eventually.” Glen added.
“I do not really see a problem,” stated Luca Brillante, “as there is not necessarily a large increase in passes with mechanical operations, as there can be in organic production, for example.”
Saving the soil
“It’s important to closely monitor soil compaction in the three zones – under vine, mid-alley and under tyre,” commented Joel Jorgensen. “Good vineyard design, with appropriate row width will help to reduce compaction in the root zone. If possible, use a smaller lighter tractor for some tasks, such as mowing – or even a ride on mower – reserving the heavier tractor when more horsepower is needed. Also consider using low impact tyres or tracks.
Glen Creasy said: “Use the largest feasible tyre size to spread the weight over a greater area, and the same with wheeled attachments. Automatic inflation and deflation equipped tyres can lower tyre pressure when driving on soil but can be raised when the tractor needs to be driven faster – or use tracks instead of wheels. Cover crops helps to increase the mechanical robustness of the soil, and avoid using tractors when the ground is wet, if possible.”
Vineyard design – key considerations
Preparation for vineyard mechanisation ideally starts before planting and uniformity is key, with consideration of row spacing, headlands, trellis design and well drained soils.
“Row width needs to suit the size of tractor to be used, so that compaction of the root zone can be minimised,” advised Joel Jorgensen. “Ensure that the headlands are wide enough, and level, for turning tractors with attachments, that anchors and cables are out of the way, and that the canopy wires are properly tensioned to avoid getting caught in machinery.
“I have come across a lot of new entrants to viticulture who are at the mercy of the tractor salesperson, who doesn’t necessarily understand the requirements for viticulture. A vineyard owner needs to think about the longer-term tractor activities and equipment needed. In a young vineyard a tractor may only be required to mow, or do other tasks with a low power requirement, but a few years later the tractor will need the power for trimmers or leaf removal – a tractor with a much higher ‘spec’. This higher ‘spec’ will involve the hydraulics, pumps, joystick, and other controls, as well as power and energy efficiencies achieved with engine management systems,” Joel continued.
“Uniformity, consistency and close tolerances are needed – as mechanisation does not play nicely with variations around what is expected,” commented Glen Creasy. “Inconsistent row widths play havoc with multiple-row equipment. Slanted vineyard posts – more likely in areas with high winds where narrow steel posts are used compared to wooden ones – can be an issue also. Trunks and shoots out of alignment will not last long,” said Glen.
The future
“I think we will have reasonably widespread use of robotic vineyard machines within 15 years. It’s probably just a few years until we get to the point where useful robotic machines are available for purchase – but at exorbitant prices!” Commented Glen Creasy. “The machines should be polyvalent and a machine, or a combination of a few machines, will be able to do pretty much any activity a human can do now. Their accuracy may not be as high as a person with experience, but they will have a place and allow work to be done around the clock. Cost of purchase will be an issue, but I suspect there will be a leasing programme to start the ‘tech’ off. Battery life will be a problem until some of the newer technologies come into play, though it will probably be feasible to install electric supply lines into the vineyard itself so that machines can work from mains electricity while in the vineyard, or use induction charging,” Glen added.
Luca Brillante agreed: “Robotic cultivation and spraying is a reality, robotic pruners are being developed, robotic harvesting as well!”
“I expect it will be many years yet before we see commercial robots. Most machines require constant vigilance from the driver so well-designed machines with good operators seem a safer bet for many years to come,” added David Sayell.
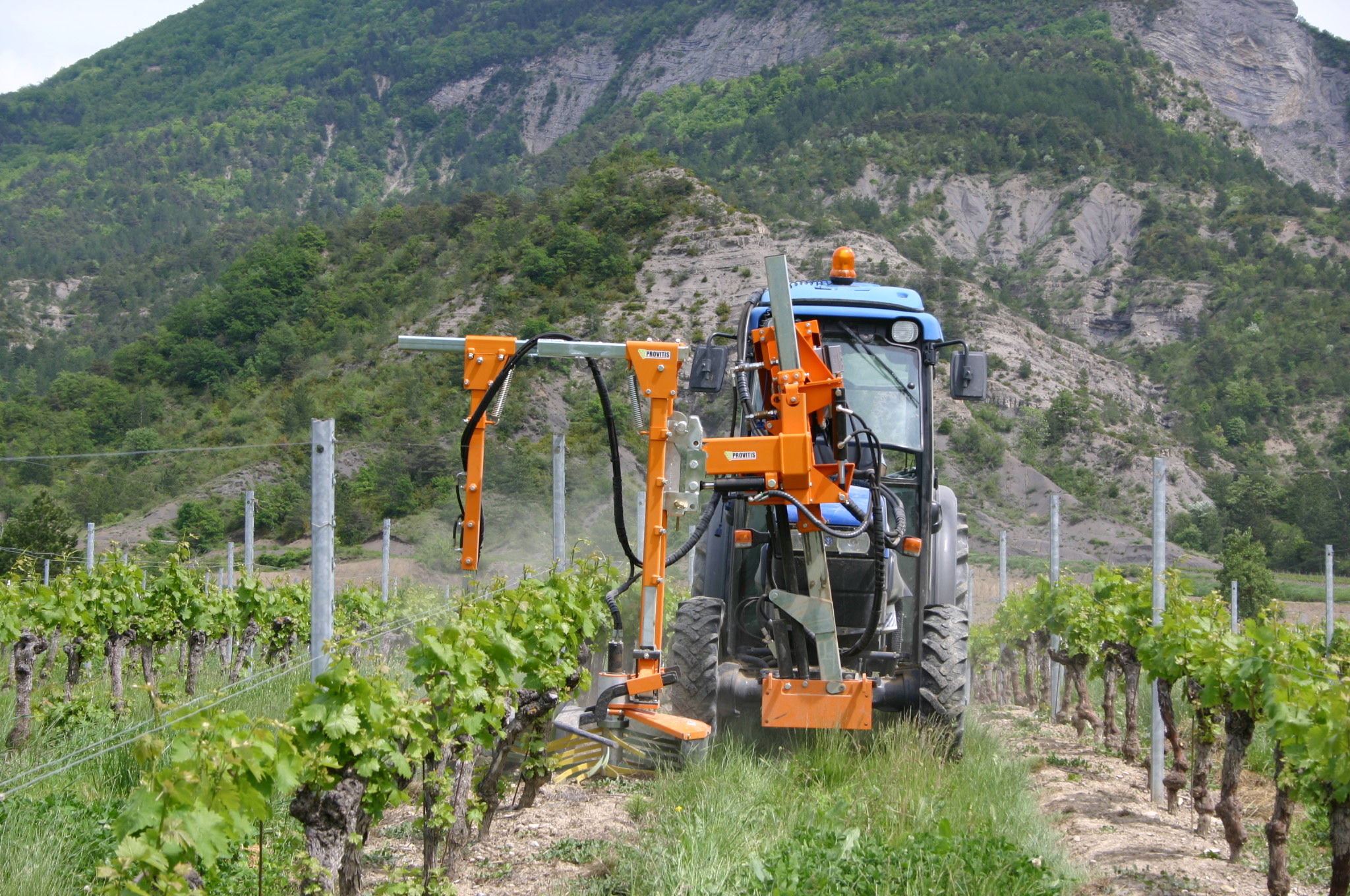
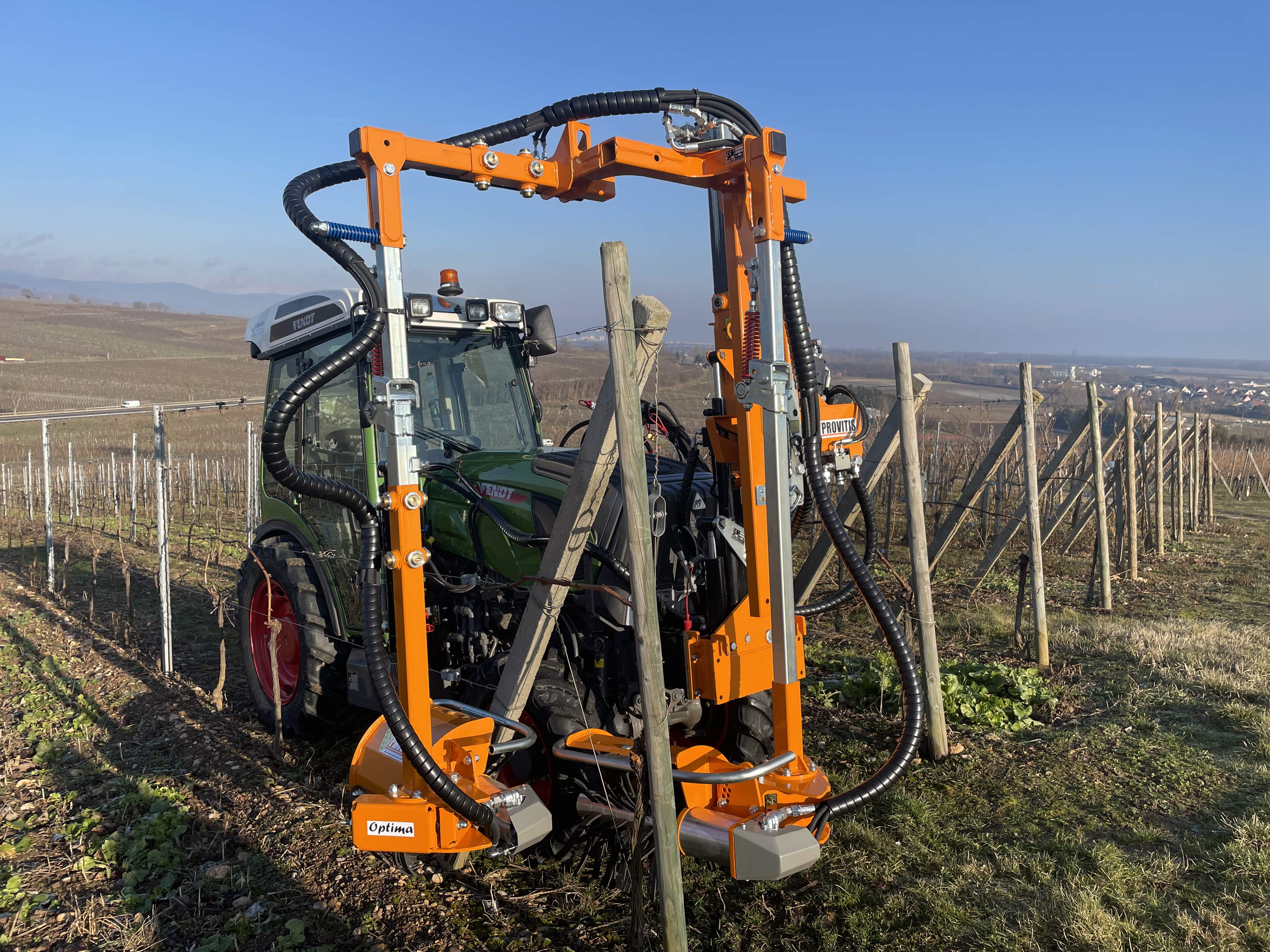
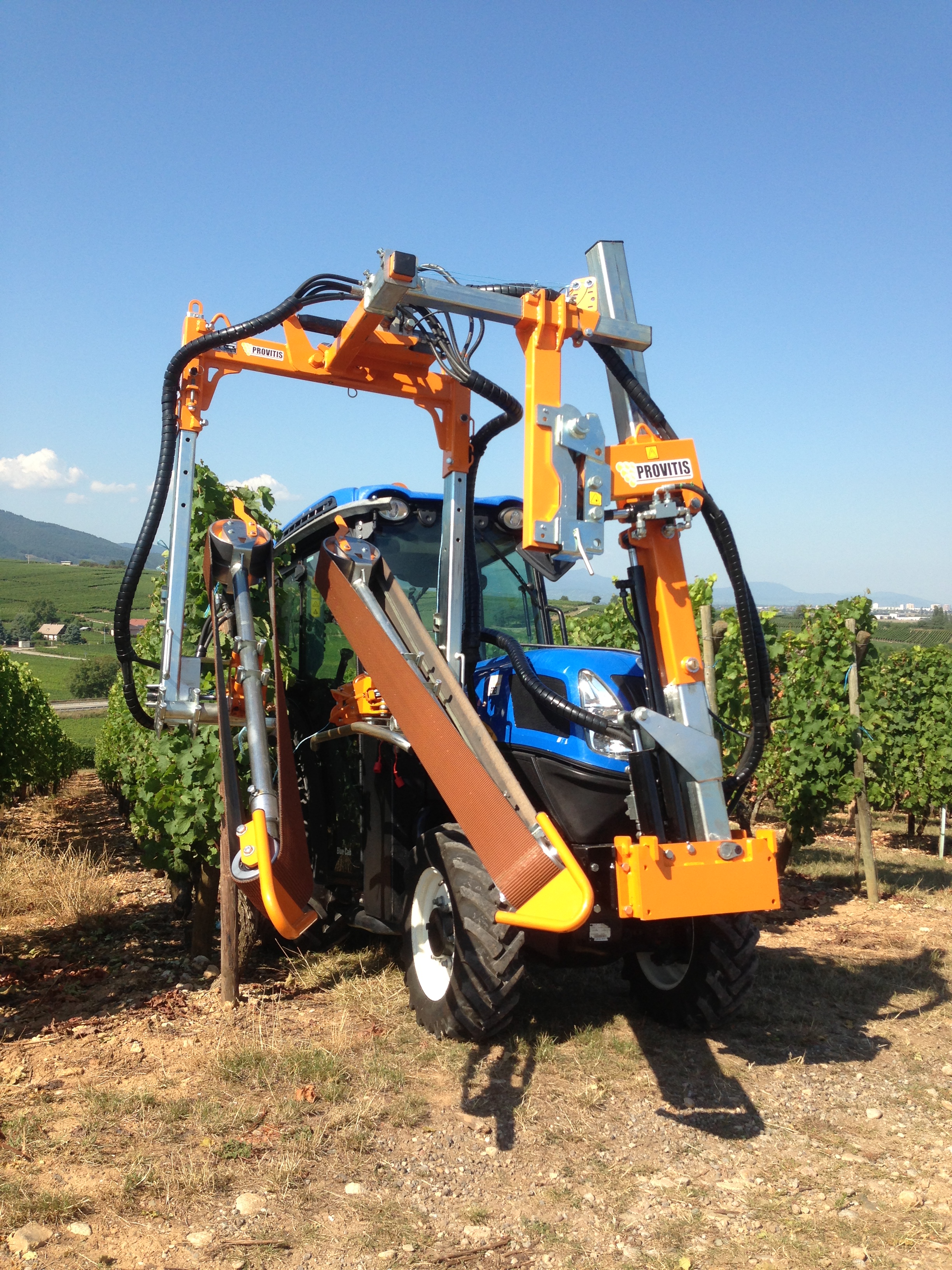

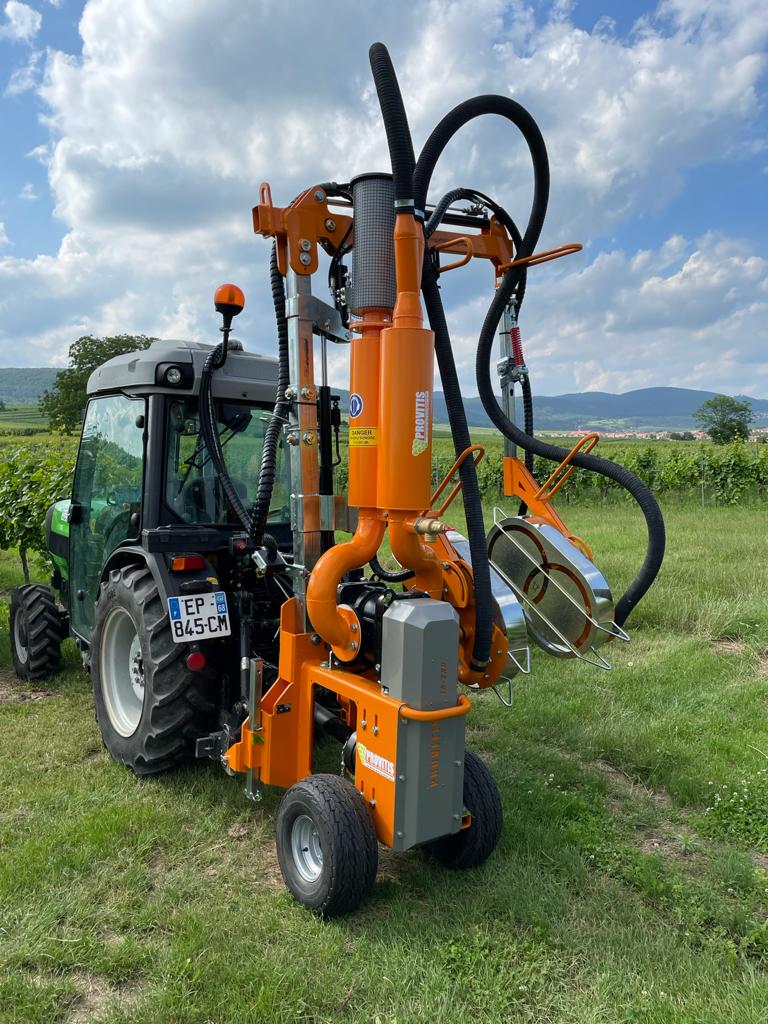
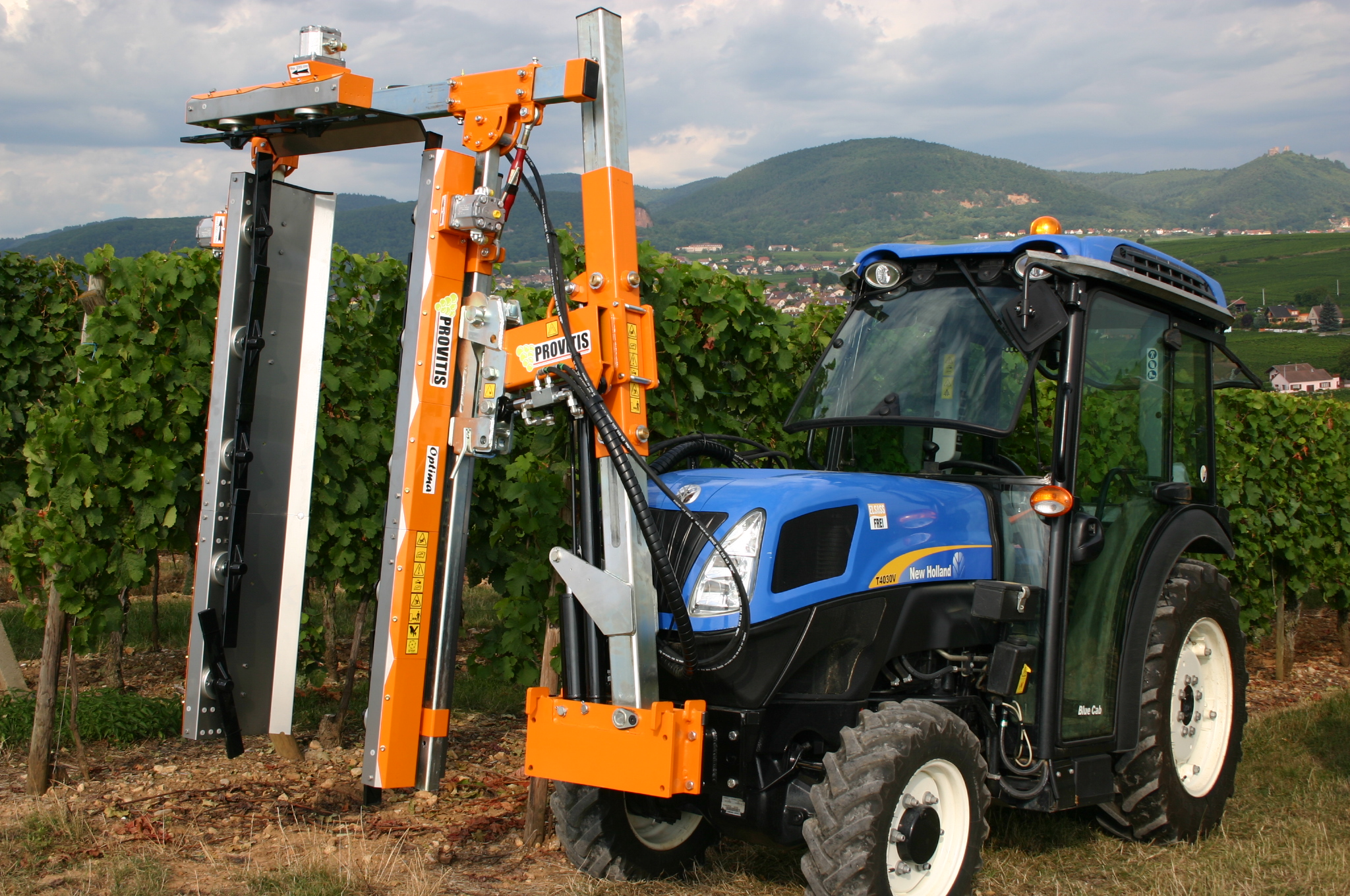
This story was taken from the latest issue of Vineyard. For more up-to-date and in-depth reports for winemakers and growers in Great Britain, read our latest issue here and subscribe here.